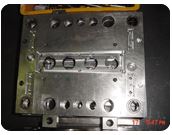
Mold
This is the frame used to melt the resin like plastic into certain shapes to mass produce the identical form of products. It is used to produce almost all the plastic products we see around us.
金型
用溶化塑料等树脂在高温高压下以一定的形态射出到金型,制造同一形态的大量制品的工序中,是普遍存在的塑料制品的加工方法,用于生产大量制品而制造而成的工具.
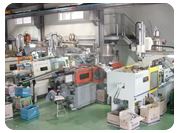
Injection
This is the process where plastic materials are heated, melted, and injected into the enclosed mold to produce products.
射出
把加温加压融化成适当的流动形态的塑料材料以高速注入到密封的金型,固化制成成型品的生产过程.
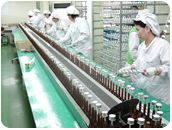
Spray Coating/Metalization
1. Air Shower: Eliminates dust from the product
2. Base Coating: protects the surface of product and adjusts the polishing of the product
3. Vacuum Metallization: The Process to create aluminum(Al) film to metallize the product
4. Top Coating: The process to protect the aluminum(Al) film and to enable various coloration work
蒸着,涂漆, 塑料射出物增加金属效果的工序
(1)空气浴:清除射出物异物的工序
(2)基础涂漆:保护射出物表面状态和调节光泽的工序
(3)真空蒸着:在射出物上形成AL膜,成金属化的工序
(4)Top涂漆:保护AL膜,可做多种颜色工艺的工序
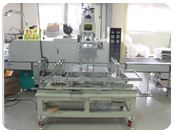
Printing
Puts the film onto the product and applies heat/pressure to transcribe the pattern on the plastic surface or puts ink in the frame with a screen and pushes the rubber panel to print.
印刷
使用印版或其他方式将原稿上的图案信息转移到产品表面的工艺.
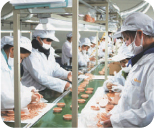
Assembly
This is the process to assemble the products after injection, vacuum metallization and printing.
组装
部件经过射出、蒸着、印刷等工序后各个附件组装在一起的工序.
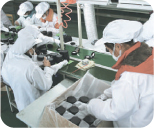
Packing
包装
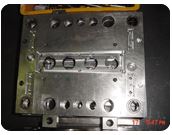
Ordering the Mold Base
– Set up the gate position
– Set up the parting line
– Set up the ejecting method
– Select a mold base format according to the product structure
设定(Mold base)
– 设定Gate位置
– 设定Parting Line
– 设定排列方式,按照制品构造选择Mold base型式
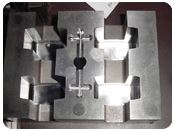
Processing
– Apply the contractile rate based on the resin
– Decide the proper machine based on the processing methods
– Select the proper cooling water point effectively
– Select pin location after considering the product shape
加工(Cove.cavity)
– 适用按照Resin的收缩率
– 按照加工法的适合的机械设定
– 有效地选定冷却水的位置
– 射出销的位置考虑产品的型像选订
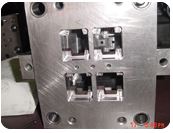
Assembling the Mold
– Assemble each of the components at the mode base
– Inspect the combination of products and the assembly status
金型组装
– 个个零件组装在Mold Base
– 查对零件的结合及组装状态
Test
– Test the molding operation
– Check the appearance of the products and size accuracy
– Check for possible problems during production in advance
测验
– 检验金型的动作顺滑与否
– 检验金型的外观及尺数精密度
– 事前核查量产时可能会发生的问题
Delivery
– Move to the following processes
出库
移动至下一工程
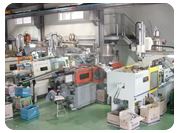
Entering the Mold
– Check the condition of operation and defects
– Check the appearance of the product and the factor of defects
– Inspect for pigment eruption
金型入库
– 检查金型动作状态及缺陷
– 检查产品外观及不良要因
– 检查金型表面清洁状态
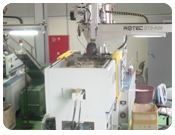
Preparing the Ingredient
– Prepare for the proper ingredient according to the setting
– Dry ingredients in advance if necessary
– Prepare the pigments in the case of color work
准备原料
– 具备适合于仕样的原料
– 操作前若需要干燥的话,实施干燥
– 若是颜色射出,准备颜料
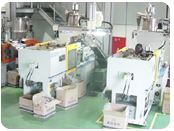
Injection
– Check the injected products periodically (molding defect, foreign substance)
– Check the operation condition of the mold
– Maintain the cleanliness of the factory
– Observe safety regulations by the workers
射出
– 有周期的检验射出物(成型不良,异物质)
– 确认金型动作状态
– 维持工厂内清洁
– 确认工作人员遵守安全守则
Packing & Inspection
– Inspect the surface of the injected products and the of the appearance
– Inspect the cleanliness for any such things as foreign substances
包装及验收
– 检查射出物表面状态及外观尺数
– 检查异物质等清洁状态
Delivery
– Move to the following processes
出库
– 移动至下一工程
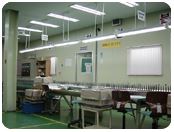
Stocking Injected Products
– Check the surface condition of the injected products
– Check the unformed and the shrinkage of products
– Check for problems such as foreign substance, dents/mark, gas and oils before coating
射出物入库
– 确认射出物表面状态
– 确认收缩及未成型等,确认有无异常
– 检查异物、磕碰、瓦斯、油等压膜前问题
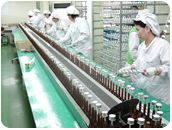
Base Coating-First Coating
[Product Setting]
– The process of preparing for the conveyor work before coating
– Check the suitability of the jig
– Check the cleanliness of the workers and the factors of defects
– Check the influence of dust and temperature
– Check the condition of the overall injection molding
[Anti-Static Gun, Air Shower]
– The process of removing foreign substances from the product before shower coating
– Remove static electricity and control the air pressure
– Adjust the driving speed
– Check the setting position
– Prevent problems such as secession from occurring (aiming at the spin frame accurately)
[UV(Base) Coating]
– The process of coating to protect the surface condition and adjust the gloss before vacuuming
[Secession]
– The process of inserting into jig bar to vacuum
– Check the condition of the membrane
– Check for the presence of the gloss
– Check for dust, foreign substance, and dryness
– Check for certain whether it is in a regular condition
下道1次镀膜
(产品定型)
– 镀膜前准备输送机操作工程
– 确认夹具是否适合
– 检查工作人员的清洁,及不良要因
– 检查灰尘及温湿度的影响
– 确认全体的射出成型状态
(无静电气枪)
– 冲洗表面,全产品去除异物工程
– 去除静电,调节气压
– 调节操纵速度
– 确认是否正确照准了被工件
– 防止发生脱离的不良品(正确安插在旋转架 )
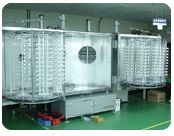
Vacuum Metalizing (Second Coating)
– The process of covering with aluminum for coating in color
– A collar various according to brilliances
– Check the degree of vacuum
– Adjust the quantity of aluminum
– Check the quantity of the product
– Check the certain the condition of the metalized products
– Check the metalizing time
– Check the condition of jig bar, and the size of the product/adjustment
UV(Base)Coating
– 真空蒸着前,为保护射出物表面状态,及调节光泽等,提供镀膜的工程
Top Coating (Third Coating)
– The process of UV coating in various colors to protect the aluminum
– The process of coating is the same as the base coating
– Check the sample color and hardness
– Check the quantity of packing box and protection paper
– Remove dust, foreign substances, and oil upon checking
– Check a identity with the sample
– Produce the same as the standard sample and notify any problems directly to the corresponding person
脱离
-为了蒸着插入JIG BAR的工程
-确认涂膜状态
-确认下道有无光
-确认灰尘,异物,干燥状态
-必须确认是否正常状态
Final Inspection & Packing(4th Process)
– Separate after the top coating (decided setting)
– Inspect products based on the limited samples
– Separately manage after classifying defects by material
– Check the quantity of the packed product (finished product packing into the box)
– Check the protective papers
– Move the packed products to the place of shipment
上道(TOP)3次镀膜
– 上道UV镀膜,保护铝膜,可用多样色彩镀膜的工程
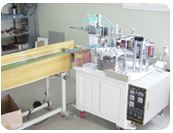
Stocking Materials
– Produce the jig according to the shape
PRINTING(丝网印刷,及标记工程图), 附材料入库
– 按照容器型像的网版制作
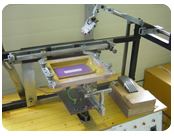
Producing the Jig
– Possess materials according with the setting
– Dry in advance if necessary
– Prepare the pigments in the case of color work
网版制作
– 具备适合仕样的原料
– 工作前需要干燥的话,实施干燥
– 若是色彩工作,准备颜料
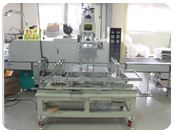
– Check the colors and printing position basis according to the standard sample
印刷
– 以标准样本为准,确认色彩,印刷位置再生产
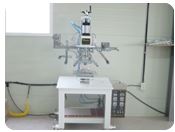
Packing & Inspection
– Pack after sorting the defects such pealing
包装及验收
– 选别印刷问题,剥离等不良品后包装
Delivery
– Move to the following processes
出库
移动至下一工程
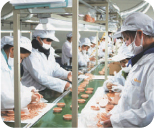
Stocking Materials
– Check the setting such as injection, vacuum, and printing based on the standard samples
辅料入库
– 把各辅料以标准样本为依据,核对射出、蒸着、印刷等各工程的作业情况
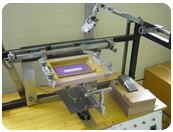
Producing the Jig
– Produce not to have defects occur both in function and appearance of the products
制作
– 在制作过程中,使产品的机能和外观不会产生不良情况
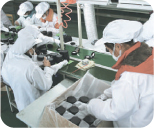
Assembling the Main Product
– Pack a standardized box with the products
装配
按作业标准准确装入对应位置
– 确认组配后功能
– 确认组配后外观状态
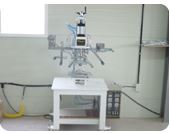
Packing & Inspection
– Follow the buyer’s requirements for both size and weight
包装及检修
– 容积和重量等遵循买主的要求
Delivery
– Move to the following processes
出厂
– 出厂
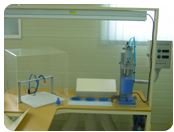
Stocking Materials
– Inspect the problems with the surface and function of the materias based on the standard sample
– Check the ingredient of the materials, color, and stability of the products
PACKING(组装工程图)
辅料入库
– 容器辅资以标准样本为准,检验容器外观及技能上的问题
– 检验原材料成分及色彩、清洁程度
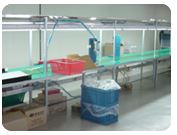
Packing
– Maintain cleanliness of the workplace
– All workers wear a sanitary coat and hat
内容物包装
– 维持工作场地的清洁状态
– 所有工作人员必须穿干净服装带上帽子
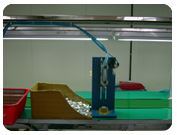
Delivery
– Delivery
出库
-出库